W jaki sposób można zoptymalizować pracę elektroerozyjnej wycinarki drutowej?
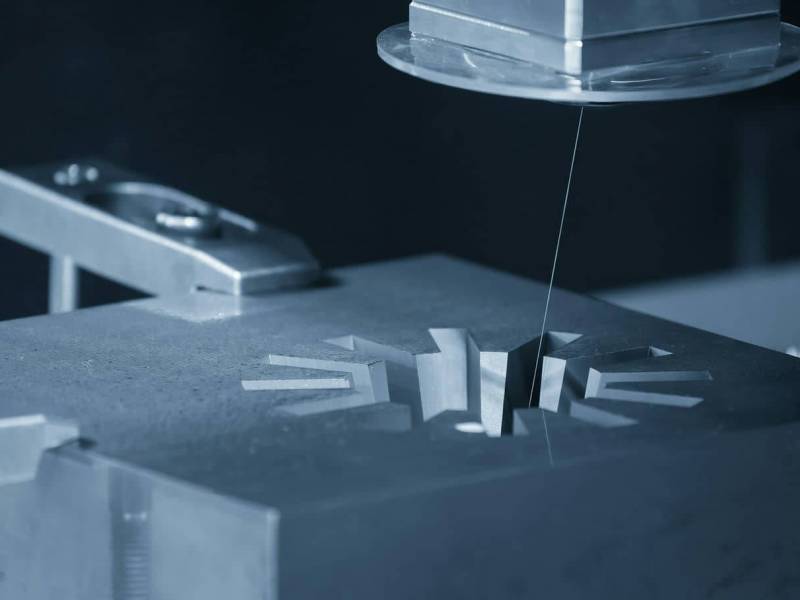
Elektroerozyjna wycinarka drutowa to precyzyjna maszyna wykorzystywana do obróbki skomplikowanych kształtów w twardych materiałach. Wydajność oraz jakość jej pracy zależy od wielu czynników, takich jak parametry obróbki, stan narzędzi czy dobór odpowiednich strategii cięcia. Aby zmaksymalizować efektywność wycinarki, warto poznać sposoby, które pozwolą usprawnić jej działanie i uzyskać najlepsze rezultaty. Elektroerozyjne wycinarki drutowe są dostępne w ofercie firmy Elektromet. Przyjrzyjmy się temu bliżej.
Dobór odpowiednich parametrów obróbki
Kluczowym elementem optymalizacji pracy elektroerozyjnej wycinarki drutowej jest właściwe ustawienie parametrów obróbki. Prąd, napięcie, prędkość podawania drutu oraz jego naciąg mają znaczący wpływ na proces cięcia. Zbyt wysoki prąd może prowadzić do nadmiernego zużycia drutu, a w konsekwencji do pogorszenia jakości powierzchni i zmniejszenia precyzji cięcia. Z kolei zbyt niski prąd może spowodować spowolnienie procesu obróbki i wydłużenie czasu pracy maszyny. Dlatego tak istotne jest znalezienie balansu między prędkością cięcia a jakością powierzchni. Również dobór odpowiedniego napięcia jest ważny, ponieważ wpływa na wyładowania elektroerozyjne oraz efektywność procesu. Kolejnym parametrem jest prędkość podawania drutu – im jest ona wyższa, tym szybciej materiał jest obrabiany, jednak kosztem precyzji. Dlatego konieczne jest dopasowanie tej prędkości do konkretnego materiału oraz zamierzonego efektu obróbki. Naciąg drutu również ma istotne znaczenie – zbyt duże napięcie może prowadzić do zerwania drutu, natomiast za małe powoduje nieprecyzyjne cięcie.
Właściwy wybór drutu i strategii cięcia
Aby zoptymalizować pracę wycinarki elektroerozyjnej, ważne jest także właściwe dobranie drutu do konkretnego zadania. Różne rodzaje drutów mają odmienne właściwości – mogą być wykonane z mosiądzu, miedzi czy stopów specjalnych. Drut mosiężny jest najczęściej używany ze względu na dobre właściwości przewodzenia prądu oraz stosunkowo niską cenę. Jednak w przypadku obróbki twardych materiałów czy wymagających dużej precyzji cięć, warto rozważyć zastosowanie drutów pokrywanych specjalnymi powłokami lub z dodatkiem innych pierwiastków, które poprawiają ich wytrzymałość. Równie istotna jest strategia cięcia – wybór odpowiedniej trasy oraz kolejności wykonywanych przejść ma bezpośredni wpływ na czas obróbki oraz końcowy efekt. Najczęściej stosuje się cięcia wielokrotne: pierwsze przejście, tzw. cięcie zgrubne, służy do usunięcia głównej części materiału, natomiast kolejne – wykańczające – mają na celu uzyskanie pożądanej jakości powierzchni i precyzji kształtu.